本場大島紬の産地、奄美大島へ
久々に休暇をとり、3泊4日で奄美大島を旅してきました。
昨年上野の都美術館で田中一村展を観て、彼が終焉の地に選んだ奄美大島に興味を持ったのがきっかけ。
島の北部にある田中一村記念美術館に訪れた後、代表作「アダンの海辺」を描いた場所かも…と思われる海岸へ行ってみたり。
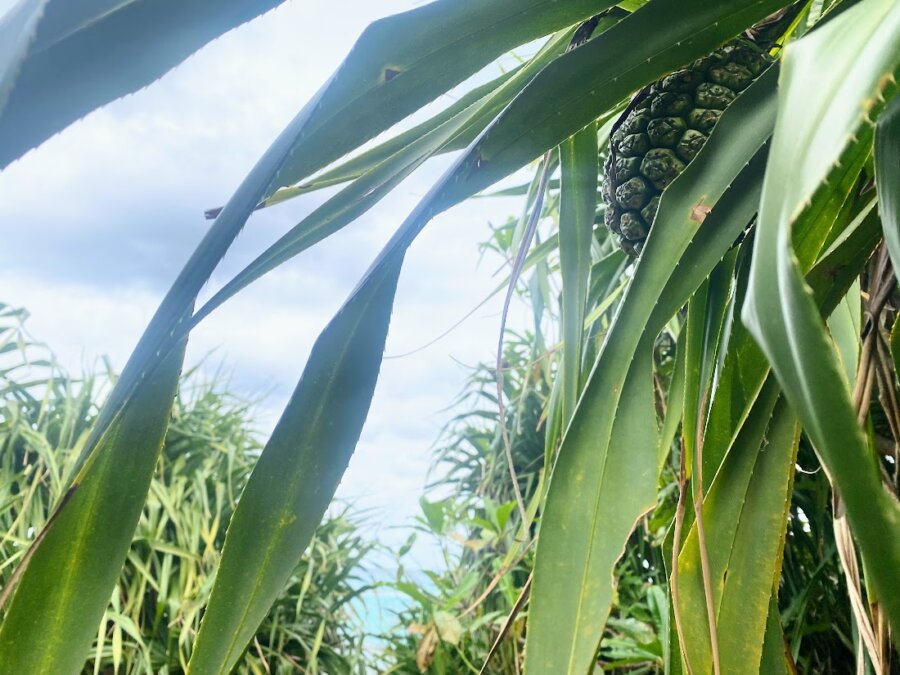
海は透明でものすごく綺麗で、亜熱帯の木々やマングローブなど自然の風景も素晴らしく、ちょうど濃いピンク色の彼岸桜が見頃でした。
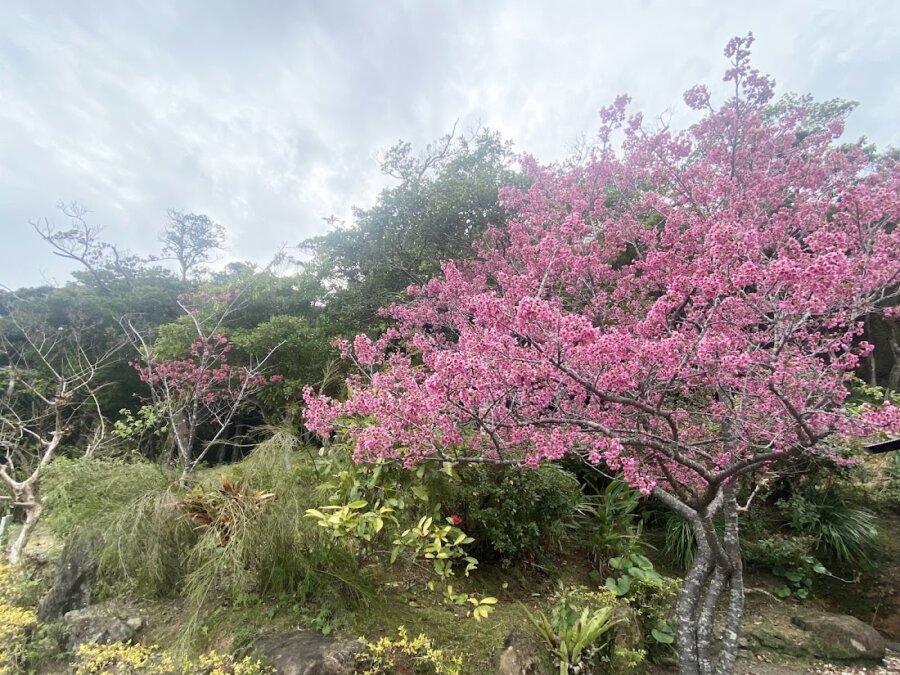
今回、時間があれば本場大島紬の生産現場も見てみたいと思っていました。
宿泊したホテルは名瀬の繁華街で、街中を散歩すると「大島紬」と掲げた商店も何軒かありましたが、ほとんどが大島紬をあしらった小物やお土産物。
もしくはシャッターが閉まっていたり、元々は呉服屋さんっぽいけれども違う商品を並べていたり。
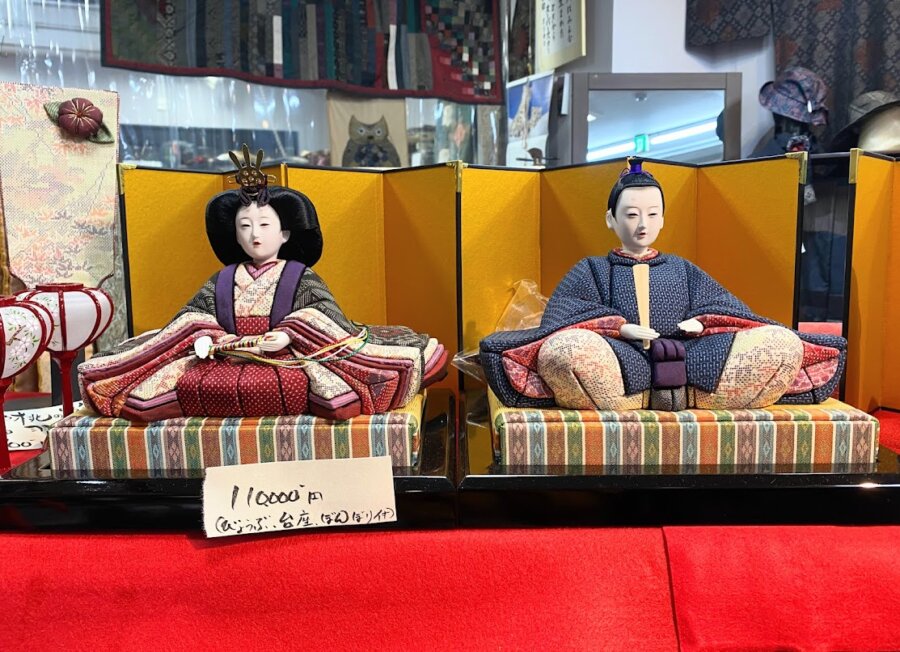
大島紬生産数の変遷
明治以前は薩摩藩への年貢として
かつて大島紬は真綿からつむいだ手紬糸を植物染料で染め、イザリ機(地機)で織られ、自家用として島民が着用していました。
江戸時代中期になると、薩摩藩より『紬着用禁止令』が出され、薩摩藩への貢物として生産されるようになります。
商品化され組合を設立
明治時代になると、大島紬が商品として取引されるようになり、需要がどんどん増えていきます。
明治34年には、鹿児島県大島紬同業組合(本場奄美大島績協同組合の前身)が設立され、製品の検査が行われるようになります。
同時期に締機(しめばた)が開発され、現在のような精巧で緻密な柄を作りだす技術も確立されます。
昭和の時代、生産数は飛躍的に増加
大正5年頃から生産数は飛躍的に伸び、昭和2年には356,094反もの大島紬が生産されています。
第二次大戦で生産数は減り、昭和20年にゼロとなったものの戦後また伸びてゆき、高度成長期を経て昭和47年には297,628反もの生産数となります。
現在は減少の一途をたどっている
ところがバブル崩壊後はみるみる減少、平成になるとさらに生産数は減り、令和5年は2,710反という状況になっています。
時代の流れによる生活スタイルの変化、着物人口の減少など要因はいろいろだと思いますが、残念なことです。
(生産数等は 本場奄美大島紬協同組合 資料より)
街を歩いていると、かつて大島紬が島の主要産業だったとわかる風景が、そこここに残っています。
戦前は島内の各集落に工場があり、約14万人が大島紬の生産に携わっていて、家庭に一人は従事していたといわれます。
日本画家の田中一村も生活のために一時期、大島紬の工場で働いていました。
大島紬が大流行したのはなぜ?
大島紬は親子3代に渡って着られるといわれるほど丈夫な織物。
前のブログでも書きましたが、私自身、祖母や母から受け継いだり、知人から譲られた大島紬を7~8枚所有しており、ふだんの仕事着からお出掛けまで大活躍しています。
とにかく軽くて着心地がよく、シワになりにくいし着付けもラク。
着物が日常的だった大正から昭和の時代に大流行して、どの家の箪笥にも大島紬が入っていたといっても過言でないかも。
これほどまで人気があったのは、機能的でお洒落という以外に何か理由があるのかな…?
たとえば映画で有名女優が着ていた、とか。
「大島紬村」で見学しました
空港でパンフレットを何種類かもらったのですが、その中から「大島紬村」へ行ってみました。
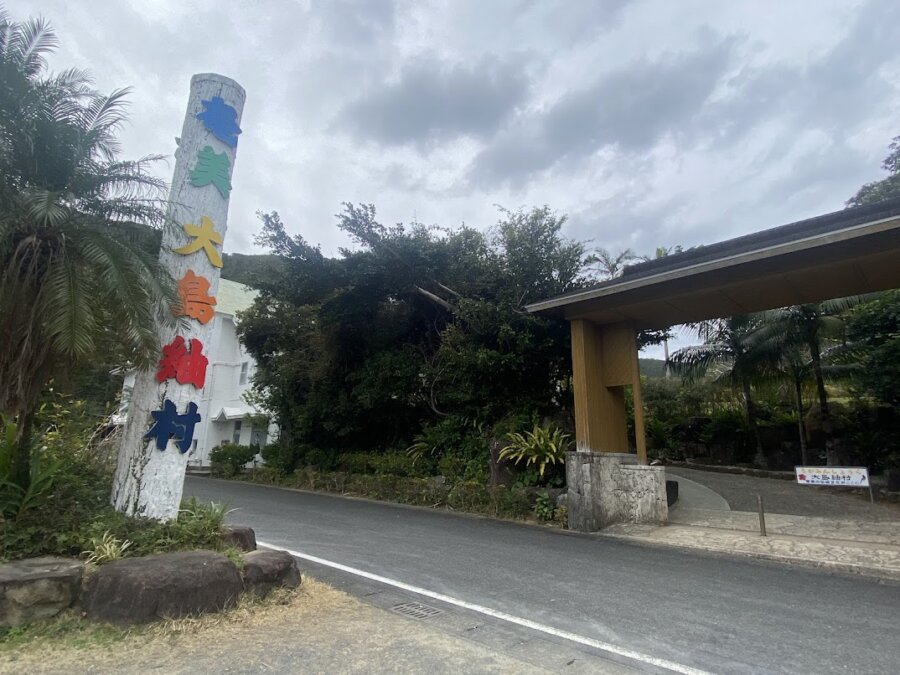
大島紬は30~40もの製造工程があり分業制ですが、こちらの会社は元々は違う場所で作業していたのを広大な敷地に集約し、製造工程を見学したり体験ができる観光スポットとしても展開しているそうです。
亜熱帯植物が生い茂る敷地に各工程の作業場があります。
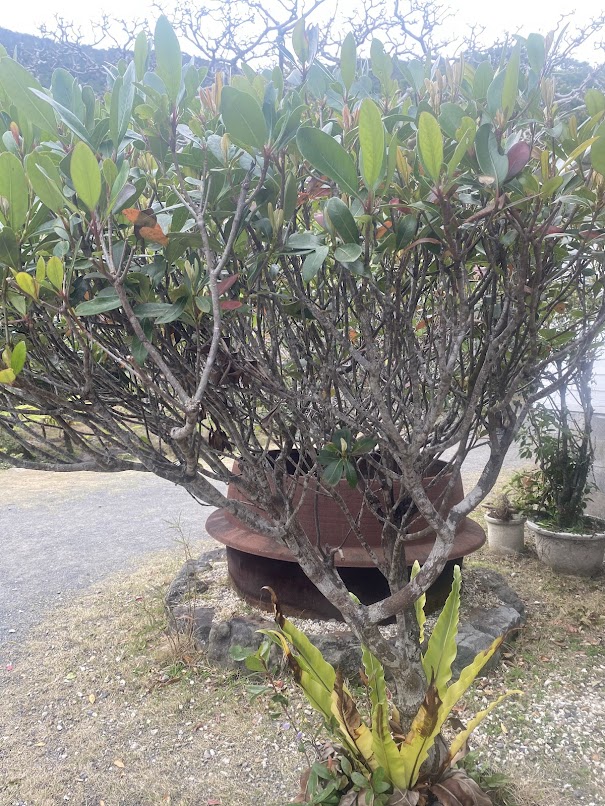
こちらは天然の泥田で職人さんが泥染めしているところ。
実際に見せていただいたのは初めてでしたが、膝まで水に浸かる大変な作業です。
昔は街中にもあって、島の人々には見慣れた光景だったそうです。
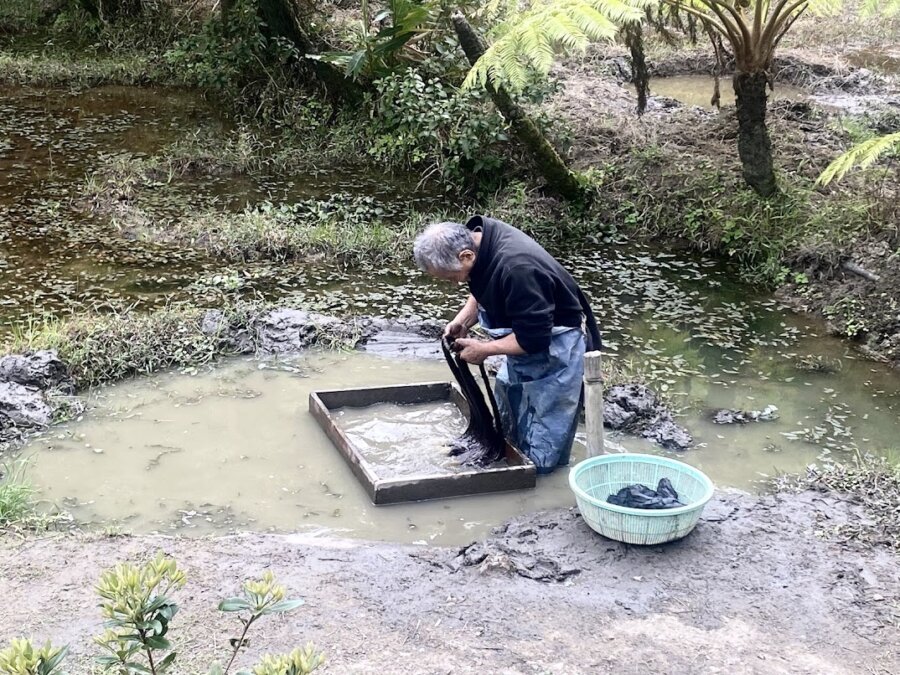
シャリンバイ(バラ科の植物)に含まれているタンニン酸色素と、泥田の中の鉄分を化学結合させることで、泥染めが出来上がります。
85回以上繰り返し染色することにより、色落ちせず、深く光沢のある渋い黒色に染まるそうです。
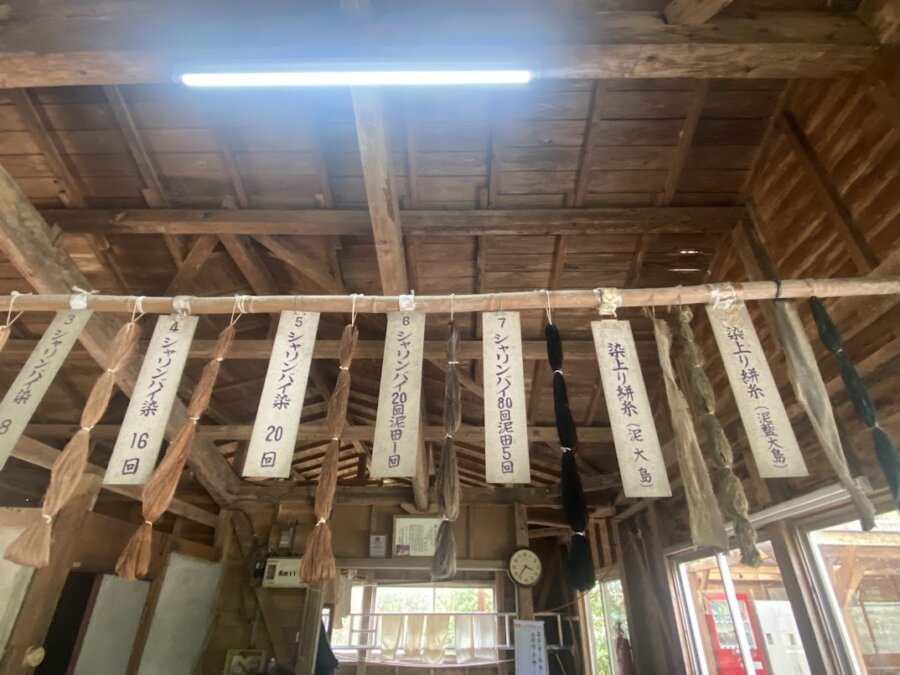
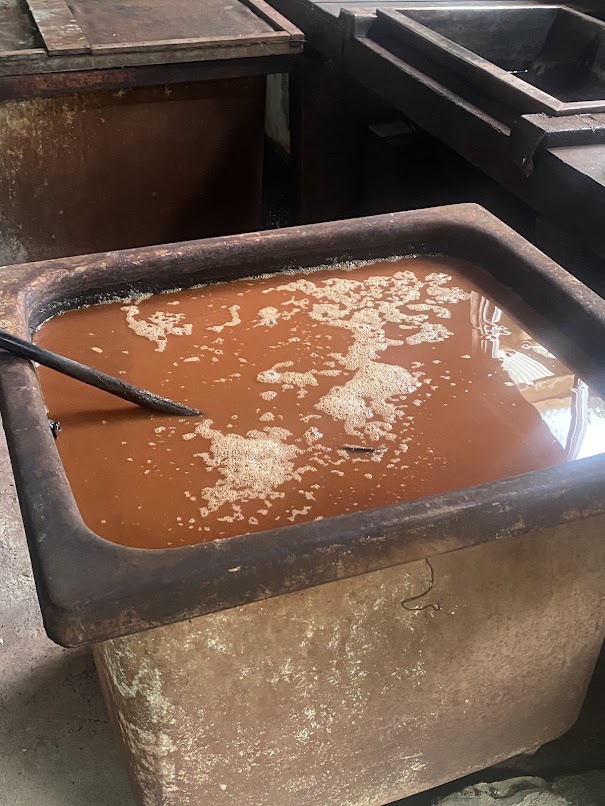
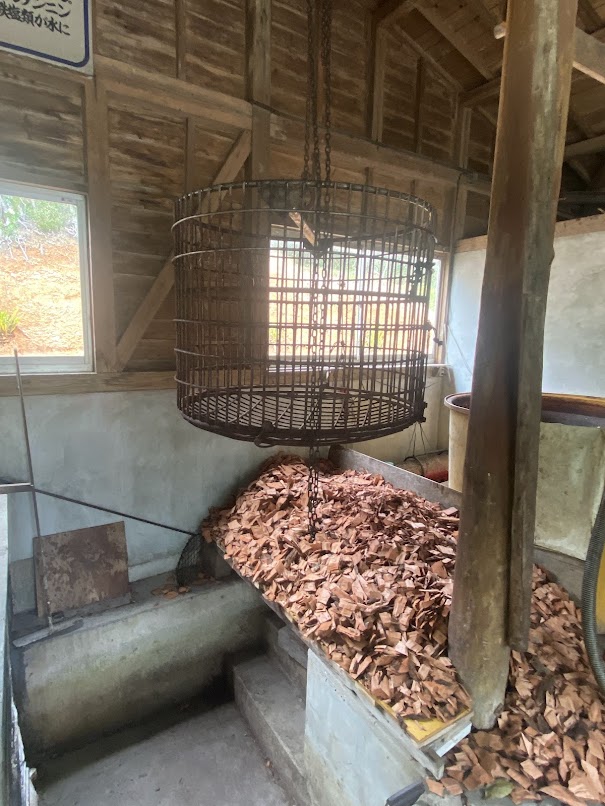
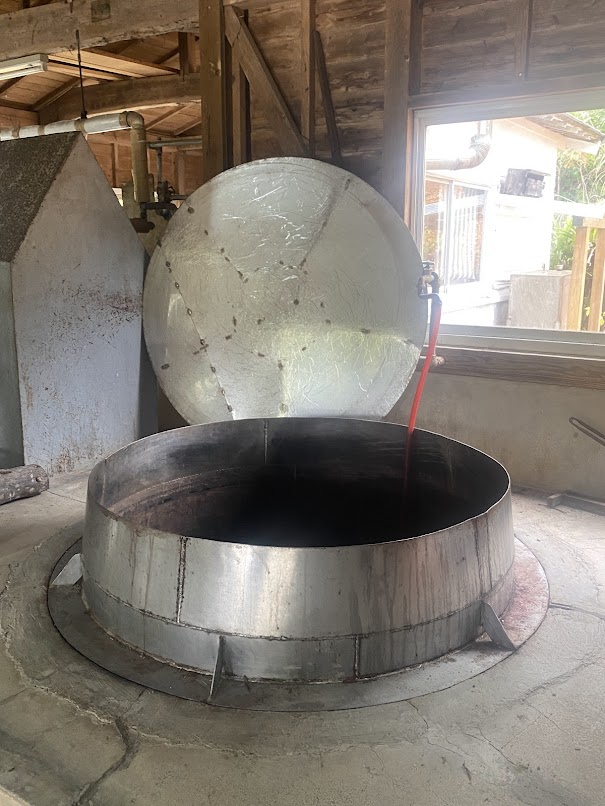
締機(しめばた)を使って木綿糸を織り込むことで、染める部分と染めない部分をつくります。
これを絣筵(かすりむしろ)といいます。
木綿糸は後で外すわけですが、かなり力も必要な工程とのこと。
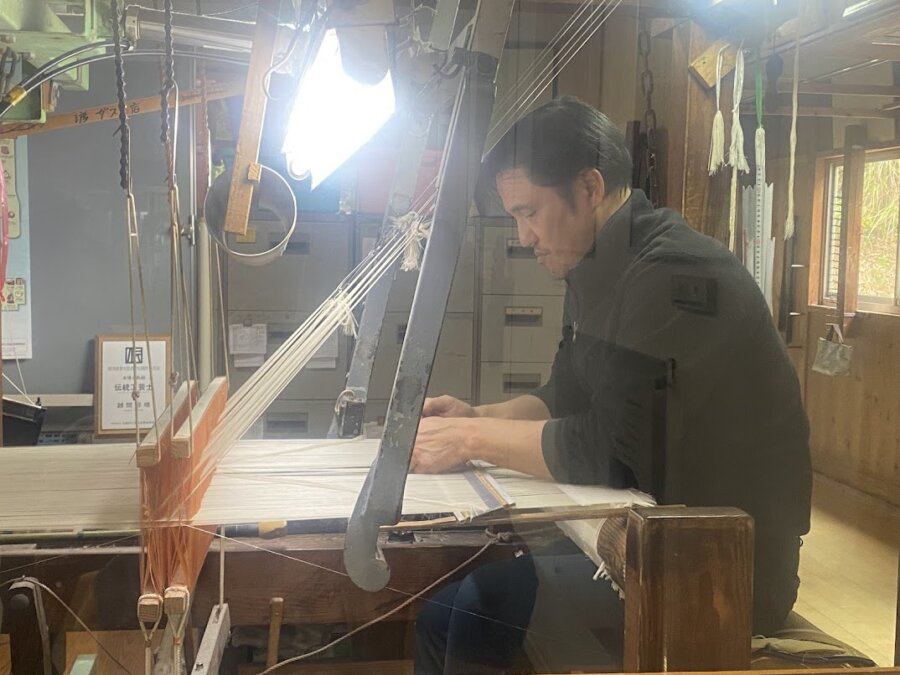
織り締めしている綿糸を切って、絣部分に染料を刷り込んでいきます。
田中一村はこの工程で働いていたようです。
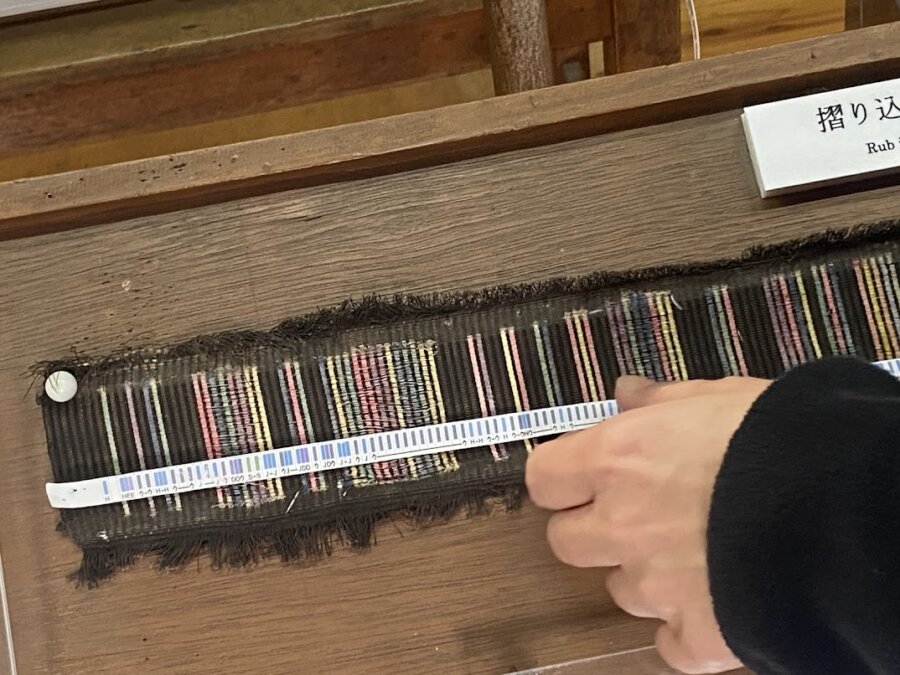
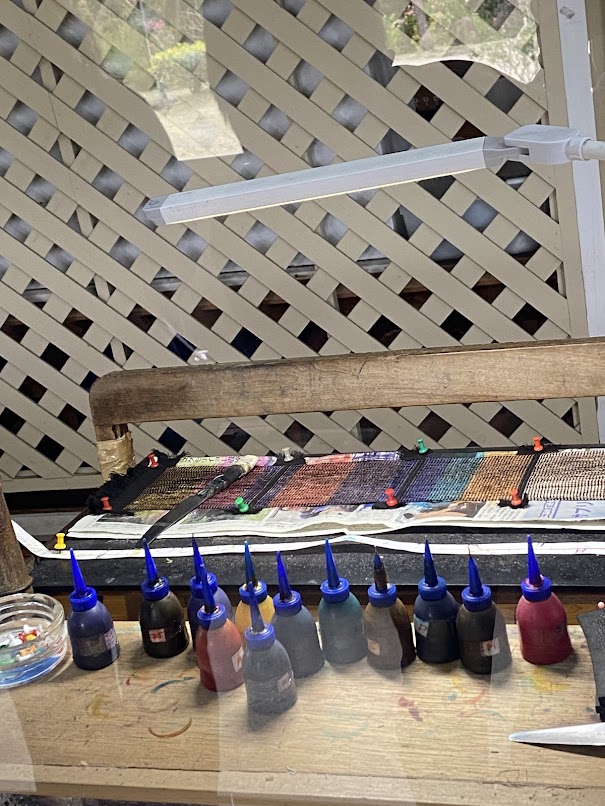
設計図に沿って織り機に糸を配列し、先染めしたたて糸とよこ糸の模様を合わせて、図案通りの柄になるように織り上げます。
もし糸が切れてしまったら、何十本もある予備の糸から同じ配置の糸を探し出して、作業を続けるそうです。まさに神業!
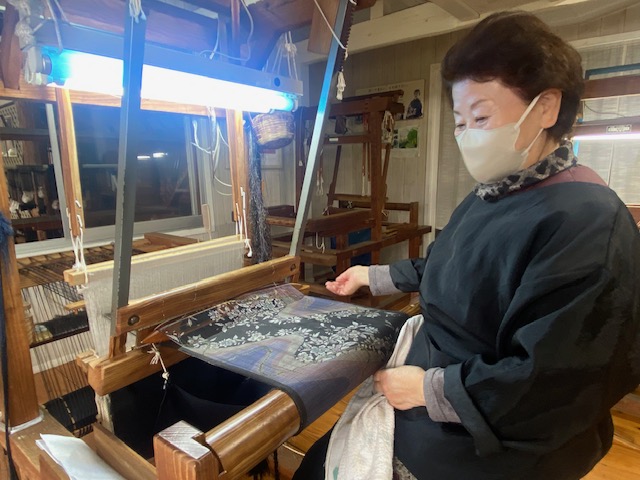
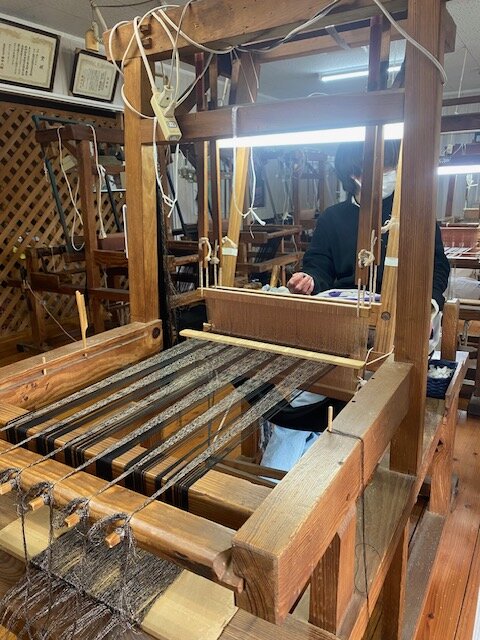
コスパ&タイパの真逆?!
昨年、銀座で着物仲間と見学した「大島紬コレクション展」でも説明を聞いたし、書籍やネットでも知識としては得ていましたが、実際に目の前で見せてもらうと、ものすごく大変な手間と時間がかかる織物だということが実感できました。
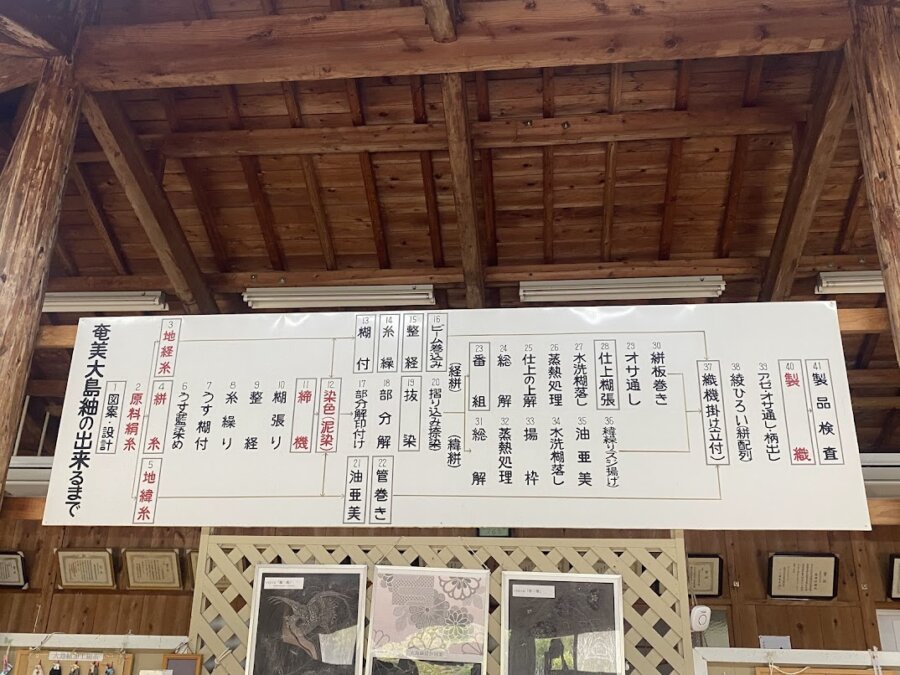
今流行りのコスパ&タイパの真逆ですね^^;
最近は高機能な化学繊維もどんどん開発されているし、プリンターを使った染め技術も発展しています。
大島紬はそういった新素材の何十倍もの時間やコストがかかるから、需要も減るし生産量も減少、各工程の職人もどんどんいなくなり…そういう現状なのでしょう。
でも、まずは着てみてほしい。
泥染めでしか出せない、この深みのある色は、日本人の肌によく似合う。
そしてからだに纏った心地よさは、着物に仕立てるからこそ体感できると思うのです。
切り刻んでしまっては、この生地の良さはわからない。
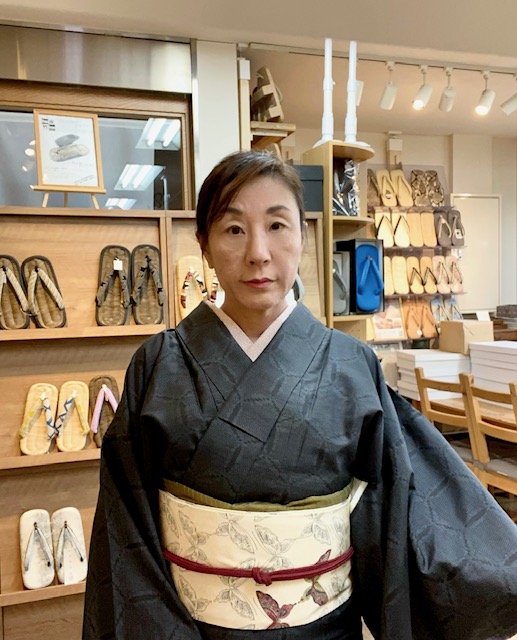
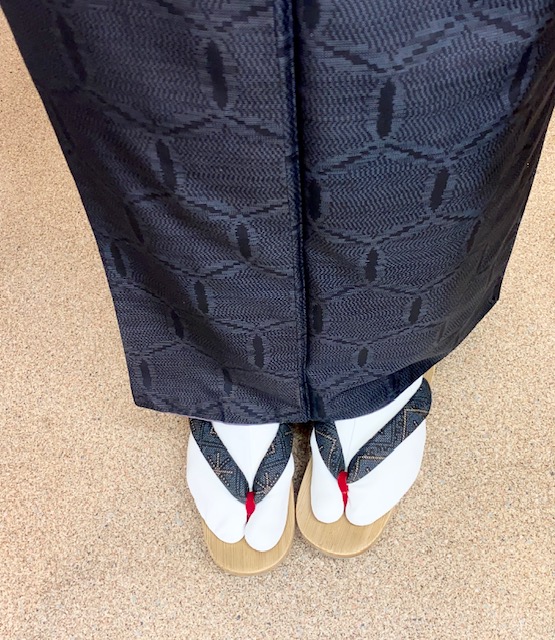
これは和装履物でもいえること。
クッション性がある新素材の草履が履きやすいと思い込んでいる人々が増えてきて、昔ながらの桐下駄や、コルク芯の革草履はどんどん需要が減っています。
しかしながら、下駄の温かみのある素材感や木肌の美しさ、革草履の軽さや革の艶やかさ…天然素材の味わいは、新素材が持っていない魅力です。
そして履き心地良さ、快適さに関しては、素材そのものよりも、鼻緒挿げの技術がもっとも大切。
当店のような専門店の職人こそが、その部分を受け持っている役目と自負しております。
コメント
コメント ( 0 )
トラックバックは利用できません。
この記事へのコメントはありません。